New MIT System can 3D Print Entire Buildings Here and on Mars
Arthur Dominic Villasanta | | Apr 26, 2017 07:41 PM EDT |
3D printing a building using a traditional method.
MIT researchers have designed a system that can 3D print the basic structure of an entire building.
This MIT technology stands to enable faster, cheaper, more adaptable building construction. Structures built with this system can be produced faster and less expensively than traditional construction methods allow, said the researchers.
Like Us on Facebook
With this technology, a building can also be completely customized to the needs of a particular site and the desires of its maker. Even the internal structure can be modified in new ways.
Different materials can be incorporated as the process goes along, and material density can be varied to provide optimum combinations of strength, insulation or other properties.
Ultimately, this approach will enable the design and construction of new kinds of buildings that wouldn't be possible with traditional building methods.
The robotic system is described this week in the journal Science Robotics. The paper was written by Steven Keating PhD '16, a mechanical engineering graduate and former research affiliate in the Mediated Matter group at the MIT Media Lab; Julian Leland and Levi Cai, both research assistants in the Mediated Matter group and Neri Oxman, group director and associate professor of media arts and sciences.
The creation of this system, which researchers call a Digital Construction Platform (DCP), was motivated by the Mediated Matter group's overall vision of designing buildings without parts.
Such a vision includes, for example, combining "structure and skin," and beams and windows, in a single production process, and adapting multiple design and construction processes on the fly, as the structure is being built.
The system consists of a tracked vehicle that carries a large, industrial robotic arm, which has a smaller, precision-motion robotic arm at its end. This highly controllable arm can then be used to direct any conventional (or unconventional) construction nozzle, such as those used for pouring concrete or spraying insulation material, as well as additional digital fabrication end effectors such as a milling head.
This free-moving system can construct an object of any size unlike typical 3-D printing systems, most of which use some kind of an enclosed, fixed structure to support their nozzles and are limited to building objects that can fit within their overall enclosure.
As a proof of concept, researchers used a prototype to build the basic structure of the walls of a 50-foot-diameter, 12-foot-high dome -- a project that was completed in less than 14 hours of "printing" time.
For these initial tests, the system fabricated the foam-insulation framework used to form a finished concrete structure. This construction method, in which polyurethane foam molds are filled with concrete, is similar to traditional commercial insulated-concrete formwork techniques.
Following this approach for their initial work, the researchers showed that the system can be easily adapted to existing building sites and equipment, and that it will fit existing building codes without requiring whole new evaluations, said Keating.
Ultimately, the system is intended to be self-sufficient. It is equipped with a scoop that could be used to both prepare the building surface and acquire local materials, such as dirt for a rammed-earth building, for the construction itself.
The whole system could be operated electrically, even powered by solar panels. The idea is that such systems could be deployed to remote regions (for example in the developing world) or to areas for disaster relief after a major storm or earthquake to provide durable shelter rapidly.
The ultimate vision is "in the future, to have something totally autonomous, that you could send to the moon or Mars or Antarctica, and it would just go out and make these buildings for years," said Keating, who led the development of the system as his doctoral thesis work.
Keating says the team's analysis shows that such construction methods could produce a structure faster and less expensively than present methods can, and would also be much safer.
TagsMIT, 3D Print, Digital Construction Platform, DCP, Steven Keating PhD
©2015 Chinatopix All rights reserved. Do not reproduce without permission
EDITOR'S PICKS
-
Did the Trump administration just announce plans for a trade war with ‘hostile’ China and Russia?
-
US Senate passes Taiwan travel bill slammed by China
-
As Yan Sihong’s family grieves, here are other Chinese students who went missing abroad. Some have never been found
-
Beijing blasts Western critics who ‘smear China’ with the term sharp power
-
China Envoy Seeks to Defuse Tensions With U.S. as a Trade War Brews
-
Singapore's Deputy PM Provides Bitcoin Vote of Confidence Amid China's Blanket Bans
-
China warns investors over risks in overseas virtual currency trading
-
Chinese government most trustworthy: survey
-
Kashima Antlers On Course For Back-To-Back Titles
MOST POPULAR
LATEST NEWS
Zhou Yongkang: China's Former Security Chief Sentenced to Life in Prison
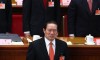
China's former Chief of the Ministry of Public Security, Zhou Yongkang, has been given a life sentence after he was found guilty of abusing his office, bribery and deliberately ... Full Article
TRENDING STORY
China Pork Prices Expected to Stabilize As The Supplies Recover
Elephone P9000 Smartphone is now on Sale on Amazon India
There's a Big Chance Cliffhangers Won't Still Be Resolved When Grey's Anatomy Season 13 Returns
Supreme Court Ruled on Samsung vs Apple Dispute for Patent Infringement
Microsoft Surface Pro 5 Rumors and Release Date: What is the Latest?