World’s First Metal 3D Printing Technology Combining Printing, Casting and Forging Developed in China
Arthur Dominic Villasanta | | Jul 23, 2016 09:00 AM EDT |
Engine part made using smart micro casting & forging.
After 10 years of research, a team of scientists in China has developed a revolutionary metal 3D printing technology that combines 3D printing, casting and forging, the first time this has been done anywhere.
The metal 3D printing technology is called "smart micro casting and forging" and the special 3D printer that gets the job done is being developed under the name, Micro Forging & Casting Sync Composite Device.
Like Us on Facebook
The technology combines metal casting and forging technology to considerably improve the strength and ductility of metal molds thereby expanding their service lives and reliability. Combining 3D printing, casting and forging also contributes to stronger parts strength and toughness; improved product lifecycles and better reliability, according to the inventors.
The Chinese team claims its new technology uses metal wire that is 90 percent cheaper than additive manufacturing powders, and is 80 percent more efficient than SLM 3D printing. It also said the technology has solved the biggest obstacle facing the 3D printing industry.
The team said its smart micro casting and forging is an innovation that will be a boon to global machinery manufacturing, the aerospace, automotive and molding industries. The technology can also be used to create thin-walled metal components while eliminating excess material.
Led by Zhang Haiou, Professor of Mechanical Engineering at Huazhong University of Science and Technology in Wuhan, Hubei province, the team also developing the Micro Forging & Casting Sync Composite Device. This all-in-one micro-casting-forging-milling manufacturing device is an alternative to metal 3D printing methods like selective laser melting and sintering.
It will be capable of producing metal forging parts up to 5.5 m × 4.2 m × 1.5 m in size with a surface roughness of 0.02 mm or the level of general machining processing.
"In the past, conventional 3D printing has been fatally flawed in the following areas. First, without forging, metal parts have a serious chance of wearing. Second, the performance of 3D printed parts has not been high. A third problem is the presence of pores and unfused portions and the fourth is that using a laser or electron beam as a heat source is very costly," said Zhang.
Experts have verified that parts made using the team's 3D printing, casting and forging all-in-one technology are more stable compared to those made by traditional casting.
Tagssmart micro casting and forging, china, Micro Forging & Casting Sync Composite Device, 3D Printing, metal 3D printing, Zhang Haiou
©2015 Chinatopix All rights reserved. Do not reproduce without permission
EDITOR'S PICKS
-
Did the Trump administration just announce plans for a trade war with ‘hostile’ China and Russia?
-
US Senate passes Taiwan travel bill slammed by China
-
As Yan Sihong’s family grieves, here are other Chinese students who went missing abroad. Some have never been found
-
Beijing blasts Western critics who ‘smear China’ with the term sharp power
-
China Envoy Seeks to Defuse Tensions With U.S. as a Trade War Brews
-
Singapore's Deputy PM Provides Bitcoin Vote of Confidence Amid China's Blanket Bans
-
China warns investors over risks in overseas virtual currency trading
-
Chinese government most trustworthy: survey
-
Kashima Antlers On Course For Back-To-Back Titles
MOST POPULAR
LATEST NEWS
Zhou Yongkang: China's Former Security Chief Sentenced to Life in Prison
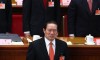
China's former Chief of the Ministry of Public Security, Zhou Yongkang, has been given a life sentence after he was found guilty of abusing his office, bribery and deliberately ... Full Article
TRENDING STORY
China Pork Prices Expected to Stabilize As The Supplies Recover
Elephone P9000 Smartphone is now on Sale on Amazon India
There's a Big Chance Cliffhangers Won't Still Be Resolved When Grey's Anatomy Season 13 Returns
Supreme Court Ruled on Samsung vs Apple Dispute for Patent Infringement
Microsoft Surface Pro 5 Rumors and Release Date: What is the Latest?